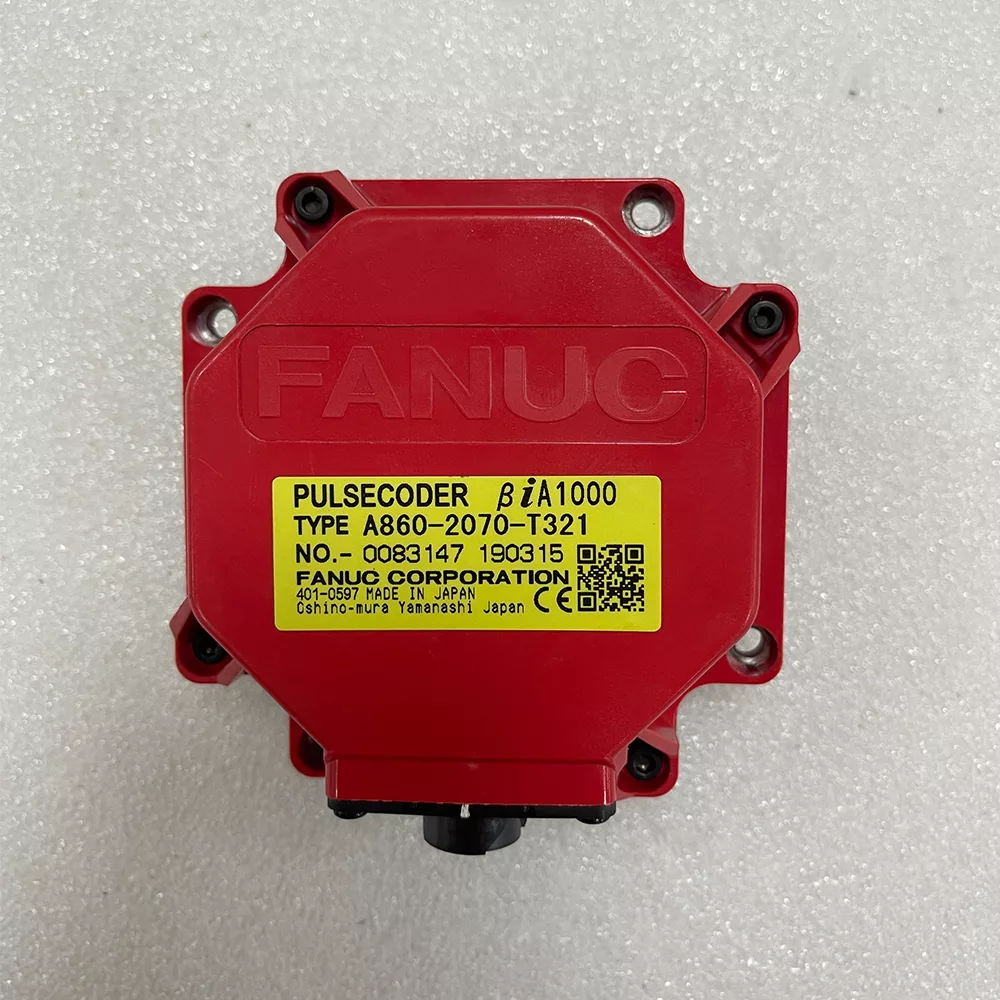
Understanding Fanuc Encoders: A Comprehensive Guide
Introduction to Fanuc Encoders
Fanuc encoders play a crucial role in the field of automation and robotics, serving as essential devices for measuring rotational or linear movement. These advanced sensors convert mechanical motion into electrical signals, which can be utilized to control and monitor the position of various components in automated systems. By providing accurate feedback on the position and speed of motors, encoders enable precise control of machinery, contributing significantly to efficiency and performance in industrial applications.
Fanuc, a predominant name in the manufacturing of robotics and automation technology, has established itself as a leader in encoder technology. The company offers a broad array of encoders designed to meet diverse industrial demands, including incremental and absolute encoders. Incremental encoders generate signals based on changes in position, making them ideal for applications where relative motion is important. On the other hand, absolute encoders provide an exact positional value, ensuring that systems retain position information even during power loss.
The applications of Fanuc encoders span a wide range of industries. In automotive manufacturing, for example, they are integral to robotic arms that assemble vehicles with precision. In aerospace, encoders facilitate the accurate movement of machinery used in the assembly and testing of components. Furthermore, Fanuc encoders are vital in semiconductor fabrication, where precise positioning is essential for intricate processes. The robustness and reliability of these encoders make them suitable for environments exposed to temperature variations and vibrations, further securing their position as industry-standard components.
As automation continues to evolve, the application and technology of encoders, particularly Fanuc encoders, remain pivotal in achieving greater efficiency and precision in various sectors. Understanding how these encoders operate helps professionals make informed choices regarding their implementation, ultimately enhancing productivity in automated processes.
Types of Fanuc Encoders
Fanuc encoders are essential components in automation and robotics, playing a critical role in motion control. There are primarily two types of Fanuc encoders: incremental encoders and absolute encoders, each with distinct working principles, functionalities, and applications. Understanding these types is crucial for selecting the appropriate encoder for specific tasks.
Incremental encoders are designed to provide relative position information. They generate a sequence of electrical pulses as the shaft rotates, allowing for the measurement of movement. The number of pulses generated directly correlates with the displacement of the encoder. These encoders do not retain position information once the power is turned off, making them suitable for applications where absolute positioning is not necessary. Their primary uses include speed control in motors and applications that require monitoring the movement of machinery in real-time.
On the other hand, absolute encoders deliver unique position information throughout the range of motion. They use a coded disc or ring to provide an absolute value of position as opposed to a relative count. Each position corresponds to a distinct digital output code, which allows for precise tracking even after a power loss. Absolute encoders are favored in situations where accuracy is paramount, such as in robotics, CNC machinery, and industrial automation systems that require consistent and reliable feedback on position.
The differences between these two types of encoders are significant, particularly in their applications. While incremental encoders are beneficial for speed and direction monitoring, absolute encoders are indispensable in environments needing precise control. Therefore, selecting the right Fanuc encoder depends on the specific operational requirements of a given application, ensuring efficiency and effectiveness in motion control systems.
Working Principle of Fanuc Encoders
Fanuc encoders play a pivotal role in motion control systems, primarily by converting mechanical motion into electronic signals that can be processed for various applications. At the core of this technology lies the principle of measurement, where the encoder determines position, speed, and direction of an object in motion. This process begins when the encoder is coupled with a rotating part, such as a shaft. As the shaft rotates, the encoder generates a series of electrical signals corresponding to its position and movement.
There are fundamentally two types of output signals produced by Fanuc encoders: incremental and absolute. Incremental encoders generate pulses as the shaft moves, allowing for the calculation of rotational changes. These pulses can be counted to determine speed and direction, but they cannot provide a specific position without a known reference point. In contrast, absolute encoders produce a unique signal for every position, retaining this data even when power is lost. This feature ensures that the system always knows its exact position upon reboot.
Resolution is another critical factor in the working of Fanuc encoders. It refers to the smallest motion change that can be detected by the encoder. Higher resolution translates to greater accuracy and precision in motion control applications, making it essential for tasks that demand fine detail, such as robotics or CNC machining. Accuracy ensures that the system consistently delivers expected results, while precision defines the repeatability of those results over time. Together, these two aspects ensure that Fanuc encoders are reliable and effective in controlling and monitoring mechanical movements, thereby playing a key role in enhancing the performance of various industrial applications.
Applications of Fanuc Encoders
Fanuc encoders play a pivotal role in various industries, significantly enhancing operational efficiency and reliability. These devices are integral to industrial automation, robotics, and CNC (Computer Numerical Control) machinery, all of which require precise motion control and feedback mechanisms. In the realm of industrial automation, Fanuc encoders facilitate seamless integration into production lines, ensuring that machines operate with minimal errors. For example, in assembly line applications, these encoders provide real-time position feedback, allowing robotic arms to adjust movements accurately, thereby increasing throughput and reducing downtime.
In the field of robotics, Fanuc encoders are commonly utilized to enhance the functionality of robotic systems. In automated warehousing solutions, robot navigational accuracy is paramount. By integrating Fanuc encoders, robotic systems are better equipped to handle the dynamic environment of warehouses, effectively managing tasks such as picking, placing, and sorting goods with precision. Case studies have demonstrated that installations utilizing Fanuc encoders show up to 30% improvement in operational efficiency compared to systems lacking such technology.
CNC machines also leverage Fanuc encoders to achieve high precision and repeatability in manufacturing processes. These machines rely on encoders to monitor the position of cutting tools and ensure that specifications are met consistently. For instance, in the aerospace industry, where the margin for error is minimal, the application of Fanuc encoders aids in maintaining strict tolerances, resulting in high-quality components that meet regulatory standards. Moreover, their robustness in high-stress environments assures manufacturers of their longevity and low maintenance costs.
Overall, the versatility and reliability of Fanuc encoders across different sectors underscore their importance in modern manufacturing and automation. As industries continue to evolve, the application of advanced encoder technologies like those offered by Fanuc will likely expand, driving further innovations and efficiencies.
Advantages of Using Fanuc Encoders
Fanuc encoders have gained recognition within industrial automation sectors for their exceptional reliability and precision. One of the primary advantages of utilizing these encoders is their ability to maintain accuracy over extended periods, which is essential for ensuring consistent operational performance in various machinery applications. The high-performance attributes of Fanuc encoders allow for real-time feedback and control, contributing significantly to the effectiveness of automated systems. This reliability minimizes the chances of equipment failure and ensures that operations run smoothly.
Robustness is another critical feature of Fanuc encoders. Designed to withstand harsh conditions, including temperature fluctuations, vibrations, and exposure to dust and moisture, these encoders can function optimally in diverse environments without compromising performance. This durability translates to longer lifecycle management and reduced maintenance efforts, which further enhances productivity while lowering operational costs.
Compatibility with other Fanuc products represents another substantial advantage of Fanuc encoders. These encoders can be seamlessly integrated into existing systems without requiring major modifications, making them an economical choice for industries already employing Fanuc technology. This compatibility fosters a cohesive ecosystem where all components work in harmony, increasing the overall efficiency of operations.
Moreover, the utilization of Fanuc encoders leads to decreased downtime, a crucial metric for any business aiming for optimal productivity. Their excellent precision and reliability ensure that machinery operates at peak performance, reducing the likelihood of errors and malfunctions. This not only prolongs the lifespan of equipment but also allows for increased output and quality within production processes, ultimately driving business success.
Common Issues and Troubleshooting Fanuc Encoders
Fanuc encoders, which play a crucial role in providing position feedback for CNC machines and robotics, are susceptible to several common issues that can affect their performance. Among these, signal loss is one of the most prevalent problems. Signal loss can occur due to a variety of factors, including interference from external noise sources, physical damage to the encoder, or issues with the connecting cables. It is essential to regularly check for loose connections or frayed wires that may contribute to this issue.
Another common hurdle encountered by users is calibration problems. Over time, encoders may drift from their calibrated settings, leading to inaccurate position feedback. This miscalibration can stem from temperature fluctuations, mechanical vibrations, or natural wear and tear. To address this, a systematic approach to recalibrating the encoder should be taken, ensuring that the procedures are followed according to the manufacturer’s specifications. Regular maintenance, including periodic calibration checks, can significantly mitigate these risks.
When troubleshooting Fanuc encoders, it is advisable to follow a step-by-step approach. Start by performing visual inspections to identify any apparent issues, such as damaged components or loose wiring. Utilize diagnostic tools to test the encoder’s output signals and confirm their integrity. If abnormalities are detected, consult the user manual or technical support for guidance on appropriate corrective actions. Moreover, implementing a routine maintenance schedule can preemptively resolve many of these issues before they escalate into more significant problems that could disrupt machinery operations.
Ultimately, addressing common issues with Fanuc encoders involves understanding the potential pitfalls and having a clear strategy for troubleshooting and maintenance. By remaining vigilant and proactive, users can enhance the longevity and reliability of their devices, ensuring optimal performance in their applications.
Integrating Fanuc Encoders into Automation Systems
Integrating Fanuc encoders into existing automation systems requires careful consideration of several factors to ensure optimal functionality and compatibility. One of the first steps involves confirming that the Fanuc encoder is compatible with the control system in use. It is crucial to consult the technical specifications of both the encoder and the controller to identify any necessary parameters. Manufacturers often provide detailed compatibility documentation, which can facilitate this assessment.
Once compatibility is verified, the next step involves proper wiring of the Fanuc encoder. Adhering to the wiring schematics provided by Fanuc is essential for minimizing the risk of electrical faults. Correctly identifying the power, signal, and ground connections is crucial for the encoder’s performance. It is advisable to use high-quality cables that are suitable for the application environment, thereby enhancing signal integrity and reducing interference.
After establishing the physical connections, configuring the software becomes the next key aspect. The encoder must be appropriately set up within the automation system’s control software. This often includes defining encoder parameters such as resolution, direction, and scaling in the system settings. It is important to ensure that the selected parameters align with the application requirements, to allow for accurate feedback and control.
Finally, facilitating seamless communication between the Fanuc encoder and the control system is pivotal. This may involve calibrating the communication protocols and ensuring that all drivers are up to date. Regular testing and troubleshooting can help diagnose potential issues that may arise during operation. By following these best practices, users can effectively integrate Fanuc encoders into their automation systems, leveraging their advanced functionality to enhance operational efficiency.
Future Trends in Encoder Technology
The landscape of encoder technology is evolving rapidly, driven by enhancements in digital devices, increased demands for precision, and the integration of emerging technologies. As we consider future trends, it is evident that Fanuc encoders specifically may play a vital role due to their reputation for quality and innovation. One key area of growth is the advancement of digital encoders. These encoders are becoming more sophisticated, utilizing higher resolution sensors that enable more accurate position and speed measurements. This increased precision can result in improved motion control in various applications, ranging from industrial automation to robotics.
Another significant trend is the integration of the Internet of Things (IoT) into encoder technology. As machines become smarter, the ability to connect encoders to the cloud for real-time data processing and analysis will enhance predictive maintenance capabilities. Fanuc devices that incorporate IoT can offer not only better operational efficiency but also provide valuable insights into the performance of machinery. This connectedness promises to streamline processes and reduce downtime, which are critical factors for businesses looking to enhance productivity.
Moreover, the impact of artificial intelligence (AI) on motion control technologies cannot be overlooked. AI algorithms can analyze data collected from encoders to optimize motion profiles, predict failures, and adapt operations in real-time. By leveraging AI, manufacturers will be able to make more informed decisions regarding maintenance schedules and operational adjustments. As these technologies become more prevalent, we can anticipate a transformative effect on how industries utilize motion control systems, specifically within the context of Fanuc encoders. The future of encoder technology will undoubtedly be characterized by enhanced efficiency, connectivity, and intelligence.
Conclusion
In summary, Fanuc encoders represent a crucial component in the landscape of modern technology, especially within automation and industrial applications. Their essential role in providing accurate position feedback and ensuring precise motion control makes them indispensable in robotic, CNC, and manufacturing processes. The performance of Fanuc encoders is deeply rooted in their engineering and design, which optimally balances reliability, precision, and durability, exemplifying their importance in operational efficiency.
As highlighted throughout this guide, understanding the various types of Fanuc encoders—such as incremental and absolute encoders—equips professionals with the knowledge to select the most suitable type for specific applications. This understanding can significantly impact the overall productivity and accuracy of projects, notably when integrated into complex automation systems. Moreover, it is imperative to consider factors like resolution, signal processing, and compatibility when choosing encoders to ensure optimized performance and seamless integration.
Consequently, readers are encouraged to explore the applications of Fanuc encoders within their own projects. Whether enhancing existing systems or designing innovative solutions, the implementation of quality encoders can greatly contribute to achieving desired results. Ultimately, selecting the right fanuc encoders, considering both quality and application requirements, will prove beneficial not just in enhancing system performance but also in driving technological advancements across various industries. Maintaining an awareness of the advancements in encoder technology will further empower professionals to make informed decisions that lead to increased productivity and efficiency in their respective fields.