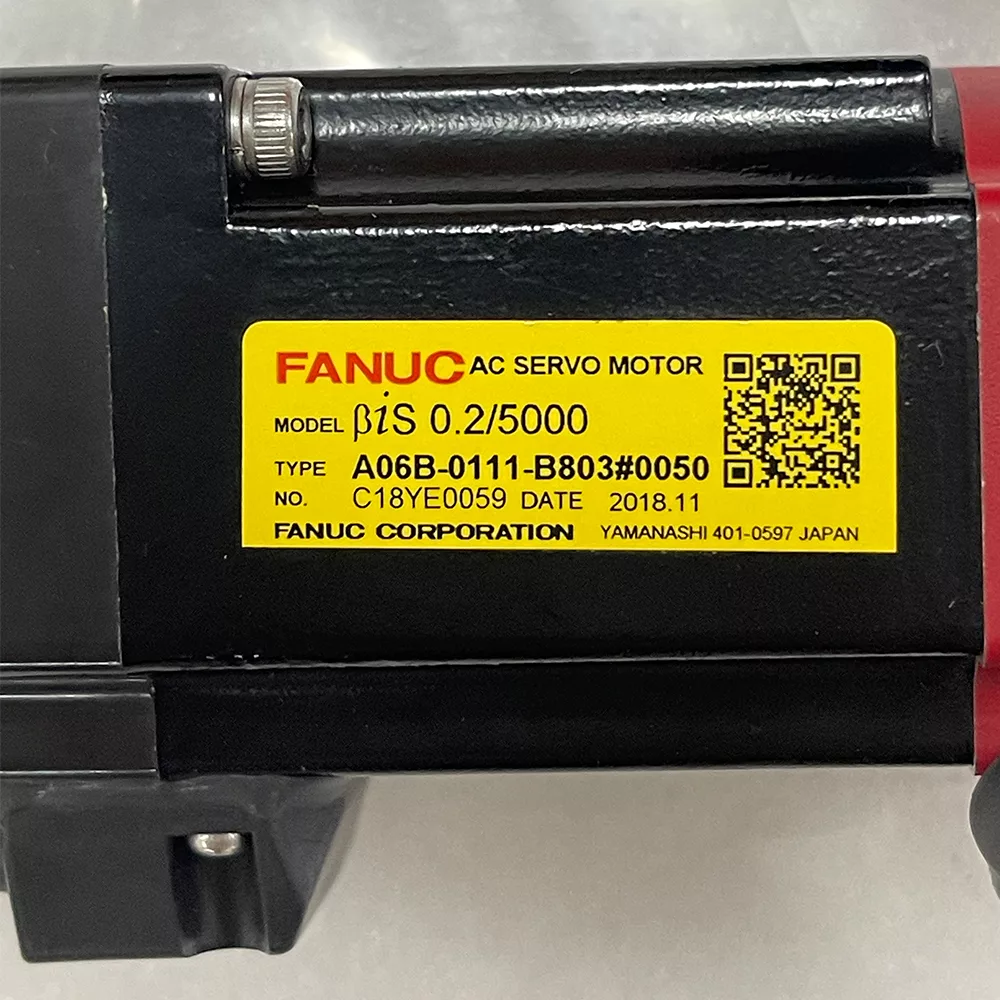
Understanding FANUC Motors: The Heart of Automation
Introduction to FANUC Motors
FANUC motors are integral components in the realm of automation, serving as the driving force behind numerous robotics and CNC (Computer Numerical Control) applications. The leading manufacturer, FANUC, has established itself as a pioneer in the industry, providing advanced solutions that enhance efficiency and precision in various sectors such as manufacturing, packaging, and assembly. FANUC motors are designed to deliver high performance, reliability, and versatility, making them suitable for a wide array of applications.
The importance of FANUC motors in automation cannot be overstated. Their technological advancements facilitate the seamless interface between machines and control systems, enabling automated processes that significantly reduce operational costs and improve productivity. These motors are engineered to provide exceptional torque and speed, which are essential for tasks ranging from simple movements to complex multi-axis operations. Additionally, the compatibility of FANUC motors with a variety of robotics and CNC systems underscores their pivotal role in today’s automated environments.
FANUC’s commitment to innovation is evident through their continuous development of motor technologies that cater to evolving industry demands. Their range includes servo motors, spindle motors, and stepper motors, each designed to meet specific operational requirements. Servo motors, for instance, offer precise control over positioning and speed, making them ideal for applications like robotic arms in manufacturing lines. In contrast, spindle motors are utilized in machining processes, where high-speed rotation is crucial for cutting materials effectively.
Overall, FANUC motors are at the core of modern automation, driving critical processes across various sectors. As industries increasingly adopt automation to enhance efficiency, the significance of these motors will continue to grow, reinforcing FANUC’s status as a leader in the robotics and CNC markets.
Types of FANUC Motors
FANUC motors are fundamental components in the automation landscape, each tailored for specific applications. Three primary types of FANUC motors dominate the market: AC servos, DC servos, and spindle motors. Understanding these categories is paramount for optimizing automation processes.
AC servo motors are known for their high efficiency and reliability. These motors are commonly utilized in environments where precise motion control is paramount. AC servos operate on alternating current and are favored for their ability to produce consistent torque across a wide range of speeds. This makes them ideal for applications such as robotic arms and CNC machines, where accuracy and repeatability are critical. Additionally, the low maintenance requirement of AC servos is a significant advantage for long-term operational efficiency.
In contrast, DC servo motors operate on direct current and are characterized by their simplicity and ease of control. These motors are particularly beneficial for applications requiring quick response times. They are often found in devices like conveyor belts and assembly line machinery, where rapid adjustments to speed and torque can enhance production efficiency. However, they may not match the efficiency or longevity of their AC counterparts, which can be a consideration for various applications.
Spindle motors are specifically designed for the rotation of tools in machining processes. They provide high torque at low speeds, essential for cutting and grinding operations. FANUC spindle motors are engineered for durability and precision, ensuring that manufacturers can maintain tight tolerances during production. Moreover, their integration into machining centers enables enhanced automation, offering greater productivity and reliability.
In conclusion, understanding the different types of FANUC motors, including AC servos, DC servos, and spindle motors, allows industries to make informed decisions. Each motor is designed with specific applications in mind, and their unique characteristics drive the efficiency and precision necessary for modern automation processes.
Key Features of FANUC Motors
FANUC motors are widely recognized as the backbone of modern automation systems due to their advanced technological features and superior performance. One of the most notable characteristics of FANUC motors is their precision. These motors are designed to deliver exceptional accuracy in positioning, which is crucial for applications that require meticulous movements, such as robotic arms and CNC machines. The precision enables manufacturers to achieve higher quality outputs, reducing waste and improving overall productivity.
Durability is another key attribute of FANUC motors. Constructed using high-quality materials, these motors are built to withstand harsh operating environments and demanding workloads. They are engineered to endure vibrations and temperature fluctuations while maintaining optimal performance levels. This robust design not only extends the lifespan of the components but also minimizes maintenance requirements, making them a cost-effective choice for industries where downtime can result in significant financial losses.
In terms of speed, FANUC motors excel by offering rapid acceleration and deceleration capabilities. This aspect is particularly advantageous for applications that require quick cycle times, allowing businesses to maintain efficiency in a competitive market. The efficiency of the motors contributes to lower operational costs while maximizing output, thus enhancing the return on investment for businesses utilizing these motors in their automation processes.
Energy efficiency is a prominent feature of FANUC motors, which is increasingly important in today’s sustainability-focused world. By utilizing advanced design techniques and technologies, such as optimized control systems, FANUC motors minimize energy consumption without sacrificing performance. This not only benefits the environment but also allows companies to reduce their energy expenses significantly.
Additionally, FANUC incorporates proprietary technologies, such as their Alpha series and iRVision systems, to enhance the performance and integration of their motors within automation systems. These technologies enable seamless connectivity and control, further solidifying FANUC’s reputation as a leader in the field of automation.
Applications of FANUC Motors
FANUC motors play a critical role in various industries, driving automation solutions that enhance operational efficiency and productivity. Their versatility allows them to be integrated into a wide range of applications, particularly in manufacturing, automotive, electronics, and healthcare sectors. In the manufacturing industry, FANUC motors are utilized in assembly lines, robotics, and CNC machines. These motors contribute to minimizing cycle times, reducing defects, and ensuring precision in machining processes, resulting in higher output and lower operational costs.
In the automotive sector, FANUC motors are essential for tasks such as welding, painting, and material handling. Their ability to perform complex operations with great speed and reliability facilitates the mass production of vehicles. Furthermore, the precision of FANUC motors ensures quality control, as they can maintain tight tolerances required in automotive manufacturing. The integration of these motors into robotic systems enhances flexibility, allowing manufacturers to adapt quickly to changing production requirements.
The electronics industry also benefits from the deployment of FANUC motors. These motors drive assembly processes for components like circuit boards and displays, where high accuracy is paramount. The automation provided by FANUC systems results in significant reductions in manual labor, thus minimizing human error and boosting the consistency of production.
Healthcare applications leverage FANUC motors in various ways, particularly in the automation of lab processes or the production of medical devices. Robotics equipped with FANUC motors can perform delicate tasks with precision, such as dispensing medications or conducting surgeries, improving patient outcomes and operational efficiency in medical facilities.
Overall, the diverse applications of FANUC motors across industries exemplify their integral role in promoting automation, enhancing productivity, and ensuring operational excellence.
FANUC Motor Specifications
FANUC motors are renowned for their robust engineering and precise performance, making them integral to various automation systems. A thorough understanding of the technical specifications of these motors is essential for optimizing their usage in diverse applications. Key specifications include power ratings, torque curves, and control systems, each of which plays a critical role in determining a motor’s suitability for specific tasks.
The power ratings of FANUC motors are typically expressed in kilowatts (kW) or horsepower (HP), indicating the amount of electrical energy converted into mechanical energy. These ratings help in evaluating the motor’s ability to handle particular loads. A higher power rating generally allows for more substantial operations and faster cycles, hence suited for applications requiring swift movements. It is important to align the motor’s power output with the operational requirements of the machinery it is powering.
Another crucial specification is the torque curve, which demonstrates how torque varies with speed. Understanding the torque characteristics of a FANUC motor can provide insights into its operating efficiency across different speeds. Motors are characterized by their maximum torque and stall torque, applicable in scenarios that require high load at startup or consistent torque throughout varied operational speeds. This makes it inherent to select a motor that not only provides adequate torque during peak demands but also operates efficiently during standard conditions.
Control systems are also a vital aspect of FANUC motors, encompassing various algorithms that govern motor performance such as acceleration, deceleration, and position control. Integration with controllers ensures that the motor operates smoothly and precisely, making the selection of an appropriate control strategy paramount in achieving desired operational outcomes. Understanding these specifications aids engineers in choosing the right FANUC motor model that aligns with both performance expectations and operational environments.
Maintenance and Troubleshooting
Maintaining FANUC motors is crucial for ensuring their efficient performance and longevity. Regular maintenance practices can significantly reduce the likelihood of operational issues and extend the active life of the motors. Key maintenance tasks include routine inspection, cleaning, and lubrication. It is advisable to inspect the motor’s external components for any signs of wear or damage. Additionally, dust and debris can accumulate over time, potentially impacting the motor’s functionality. Regular cleaning not only helps maintain performance levels but also prevents overheating caused by obstructed cooling paths.
Lubrication is another vital practice in the upkeep of FANUC motors. The bearings within these motors must be properly lubricated to minimize friction, reduce heat generation, and prevent premature wear. Users should consult the manufacturer’s guidelines to determine the appropriate lubricant type and frequency of application. Adhering to these recommendations will ensure optimal performance and reduce the risk of unexpected failures.
In the event of motor malfunction, familiarity with common troubleshooting techniques can be beneficial. Some frequent issues include unusual noise, overheating, or erratic performance. Unusual noises may indicate mechanical issues, such as bearing failure or misalignment, which require prompt attention. Overheating can stem from insufficient cooling or improper lubrication, while erratic performance may suggest electrical issues or sensor malfunctions.
For effective troubleshooting, users should first verify all electrical connections, as loose or corroded connections can lead to power loss or erratic behavior. Additionally, checking for any fault codes that the motor might display can provide insights into underlying issues. If the problem persists, it is prudent to refer to the manufacturer’s documentation or consult with a qualified technician to ensure a thorough diagnosis. Through diligent maintenance and prompt troubleshooting, users can maintain their FANUC motors’ peak performance and reliability.
Integrating FANUC Motors with Automation Systems
In the realm of automation, the integration of FANUC motors plays a pivotal role in achieving optimal performance and efficiency. These motors are designed to work seamlessly with various automation systems, such as Programmable Logic Controllers (PLCs), Computer Numerical Control (CNC) systems, and robotic applications. Understanding the nuances involved in this integration is essential for maximizing the capabilities of automation technology.
When connecting FANUC motors to PLCs, one must consider communication protocols and network configurations. FANUC motors typically support various communication standards, including Ethernet/IP, Profibus, and CANopen, allowing for flexible integration within diverse automation environments. Proper setup ensures that the PLC can effectively send and receive control signals, facilitating real-time monitoring and adjustment of motor functions. This enhances operational responsiveness and aligns with the demands of complex manufacturing processes.
Incorporating FANUC motors into CNC systems requires precise calibration and synchronization. The motors’ performance characteristics must align with the CNC controller to ensure accurate positioning and movement. Factors like smoothing algorithms and acceleration profiles are crucial for maintaining the desired operational standards. Moreover, software tools provided by FANUC can aid in programming and optimizing motor parameters, resulting in decreased cycle times and improved product quality.
Robotics applications further highlight the versatility of FANUC motors. When integrated with robotic systems, these motors contribute to the dynamics of motion and precision control, essential for tasks such as assembly, welding, or material handling. It’s important to configure the robot controller and FANUC motors to establish a cohesive relationship between the two, ensuring that the entire system operates harmoniously.
Effective integration of FANUC motors within automation systems is contingent upon careful planning, appropriate communication protocols, and meticulous programming. By addressing these considerations, operators can unlock the full potential of FANUC motors, fostering a robust and efficient automated environment.
Future Trends in FANUC Motors
The future of FANUC motors is poised for significant transformation as technology continues to evolve. One of the most prominent trends is the integration of the Internet of Things (IoT). This development facilitates enhanced connectivity, allowing FANUC motors to communicate with other machines and systems in real-time. Such data exchange can improve efficiency and optimize operations by enabling predictive maintenance, thereby reducing downtime. As industries increasingly rely on automation, the incorporation of IoT capabilities into FANUC motors will provide a competitive edge through smart manufacturing solutions.
Moreover, the trend towards increased automation is reshaping the landscape for FANUC motors. Industries, including automotive, electronics, and pharmaceuticals, are embracing automated processes to boost productivity and minimize human error. FANUC motors are becoming integral to robotic systems and automated machinery, allowing for greater precision and speed. This increase in automation not only enhances efficiency but also significantly reduces operational costs. As companies aim for higher output levels, the demand for advanced FANUC motor technology will continue to grow.
Advancements in motor design are another critical area of development. Ongoing research in materials science and engineering is leading to the creation of lighter, more efficient, and durable motors. These innovations also focus on energy efficiency, which is essential in sustainable manufacturing practices. Energy-efficient FANUC motors can significantly lower operational expenses and contribute to an organization’s sustainability goals. As environmental regulations and consumer demand for green practices increase, manufacturers will likely adapt their processes around such technologies, marking another pivotal shift in the industry.
In conclusion, the future of FANUC motors is being defined by exciting advancements in IoT integration, increased automation, and innovative motor designs. As these trends gain momentum, they are set to redefine industry standards, making FANUC motors not only essential components but also vital contributors to the future of manufacturing.
Conclusion
FANUC motors serve as a pivotal component in the realm of automation, playing an essential role in various industrial applications. These motors are renowned for their precision, reliability, and efficiency, making them a favored choice among manufacturers looking to enhance productivity and improve operational performance. With seamless integration into robotic systems, CNC machines, and more, FANUC motors offer the agility and responsiveness required to meet the demands of modern manufacturing processes.
The benefits of incorporating FANUC motors into automation systems are numerous. They not only significantly reduce downtime with their high durability and low maintenance requirements but also contribute to energy savings, thereby supporting sustainable manufacturing practices. As industries across the globe continue to embrace automation, the importance of these motors cannot be overstated. They enable complex tasks to be executed with remarkable accuracy, contributing to both the quality and consistency of production outputs.
As we look toward the future, the evolution of FANUC technology is poised to bring even more advancements to the forefront of automation. With ongoing research and development, the potential for enhanced performance and smarter integration with artificial intelligence is on the horizon. This progress signifies that businesses should consider incorporating FANUC motors not just for current automation needs but also as a foundational element for future-ready operations. In embracing these cutting-edge technologies, companies can position themselves competitively in an increasingly automated world.