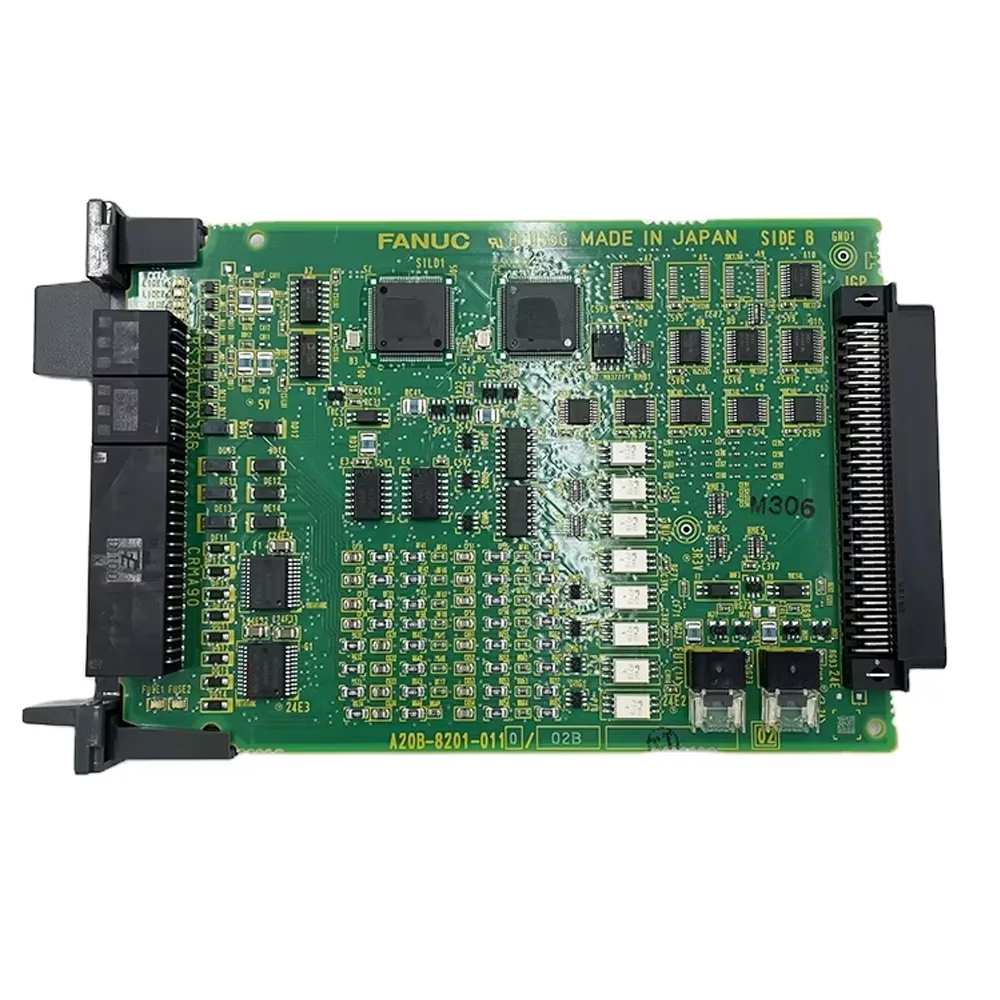
Understanding FANUC PCB: A Deep Dive into its Components and Applications
Introduction to FANUC PCB
The FANUC PCB (Printed Circuit Board) serves as a fundamental component in the realm of automation and robotics, playing a crucial role in the performance and functionality of FANUC machines. These circuit boards are essential for facilitating communication between various electronic components, ensuring that machines operate smoothly and efficiently. In an industry increasingly reliant on automation, the significance of FANUC PCBs cannot be overstated.
FANUC, a pioneer in the field of industrial automation, utilizes PCBs to integrate complex systems within its products. These circuit boards are designed to house microcontrollers, sensors, and other vital electronic elements that govern the behavior of robotic systems and CNC machines. By ensuring reliable connections and signal transmission, FANUC PCBs help enhance productivity and precision in manufacturing processes.
The design and manufacture of FANUC PCBs are tailored to meet the demands of modern manufacturing environments. Given the need for high-speed processing and real-time control in automated operations, these boards are engineered to withstand rigorous performance criteria. This emphasizes their importance not just in functionality but also in longevity and durability, which are crucial for minimizing downtime and maintaining operational efficiency.
Moreover, the versatility of FANUC PCBs enables their application in various sectors, from automotive to electronics and beyond. Whether controlling robotic arms, coordinating motion systems, or managing different operations in manufacturing lines, the role of PCBs is paramount in ensuring that FANUC machinery meets the diverse and evolving needs of industries worldwide. As technology progresses, the ongoing development of FANUC PCBs will continue to shape the future of automation, driving innovation and efficiency across multiple sectors.
Key Components of FANUC PCB
The printed circuit board (PCB) is an integral component of FANUC systems, serving as a foundation for connecting various electronic elements essential for optimal performance. At the core of any FANUC PCB is the microcontroller, which acts as the brain, executing programmed instructions and managing the operations of the equipment. These microcontrollers are specifically designed to handle complex algorithms necessary for precise control in industrial automation tasks.
Another pivotal component is the interface circuitry, which facilitates communication between the microcontroller and other system elements. This includes both digital and analog interfaces, enabling interaction with sensors and user inputs. By converting signals to a suitable format, the interface circuitry ensures accurate data transmission, thus enhancing overall system responsiveness.
Power supply circuits are equally crucial, as they regulate and distribute electrical power throughout the PCB. Typically, FANUC PCBs contain various power conversion elements, including voltage regulators and capacitors, which stabilize and filter the power supply, ensuring that all components receive a consistent and reliable energy source. This is vital for the longevity and stability of the equipment.
Furthermore, sensor inputs play a fundamental role in enabling the equipment to respond to its environment. These sensors provide real-time data on various operational parameters, such as position, speed, and temperature. By integrating this information, the microcontroller can make instantaneous adjustments, improving efficiency and safety in industrial operations.
In summary, understanding the key components of FANUC PCBs—microcontrollers, interface circuitry, power supplies, and sensor inputs—highlights how each element contributes to the robust performance and reliability of FANUC’s automation solutions. Each component’s specific function ensures seamless operation within complex industrial environments.
Types of FANUC PCBs
FANUC PCBs (Printed Circuit Boards) are integral components utilized across a wide range of machines, serving distinct functions based on their design and intended applications. These circuit boards can be categorized into several types, each tailored to meet specific operational criteria. Understanding the different types of FANUC PCBs is crucial for professionals in the automation and manufacturing sectors.
One of the primary categories of FANUC PCBs is the control PCB. Control PCBs manage the commands and processes within machinery. They facilitate communication between the central processing unit (CPU) and various machine components. For example, in robotic arms, the control PCB interprets the programmed tasks and ensures accurate execution. This type of PCB plays a vital role in maintaining the precision and responsiveness of automation systems.
Another significant category is the communication PCB. These boards are responsible for enabling data transfer between different components and systems. In environments where machines must interact with each other, communication PCBs ensure seamless integration with networks, other machines, and user interfaces. This facilitates real-time monitoring and adjustments, enhancing operational efficiency and reducing downtime.
Power management PCBs are also essential within FANUC systems. These boards handle the distribution and regulation of electrical power throughout the machine. By managing voltage levels and ensuring stable power supply, power management PCBs protect sensitive components from potential damage and contribute to the overall reliability of the machine.
In conclusion, categorizing FANUC PCBs into control, communication, and power management types underscores their diverse functionality within automation systems. Each type serves a specific purpose, making it crucial for engineers and technicians to select the appropriate PCB based on the machine’s requirements and applications. Proper understanding of these components enhances operational efficiency and performance within the manufacturing environment.
Manufacturing and Design Process of FANUC PCB
The design and manufacturing of FANUC PCBs involve a meticulous process that prioritizes reliability and performance. The initial phase encompasses the conceptualization of the printed circuit board, where engineers utilize advanced design methodologies such as schematic capture and layout design. These processes ensure that the PCB effectively supports the intended functionality of the component within the larger FANUC system.
Material selection is a crucial aspect of the design phase. FANUC PCBs are typically constructed using high-quality materials that can withstand rigorous industrial environments. Common materials include FR-4, a composite of woven glass fabric and epoxy resin known for its excellent electrical insulation properties and thermal stability. Additionally, when high-frequency performance is necessary, materials such as Rogers or Taconic may be employed due to their superior dielectric properties.
Once the design is finalized, the manufacturing process commences. It generally includes several key steps: photolithography, etching, drilling, and plating. In photolithography, a photosensitive material is applied to the PCB surface, allowing the circuit pattern to be transferred. Following this, etching removes unwanted copper, revealing the required circuitry. Drilling allows for the creation of vias and component mounting holes, which are essential for assembling electronic components. Finally, plating adds a thin layer of gold or other metals to enhance conductivity and prevent oxidation.
Throughout the manufacturing process, adherence to industry standards such as IPC-A-600 and IPC-2221 is strictly maintained. These standards outline the requirements for the design and qualification of PCBs, ensuring consistent quality and reliability during operation. By combining rigorous design methodologies, high-quality materials, and comprehensive fabrication processes, FANUC PCBs are engineered to meet the demands of various applications within automation and robotics, reflecting a commitment to excellence in manufacturing.
Troubleshooting Common Issues with FANUC PCBs
FANUC Printed Circuit Boards (PCBs) are integral to various industrial applications, often controlling essential functions in automation processes. However, like any electronic component, FANUC PCBs may encounter issues that can compromise their performance. Frequent problems include signal degradation, component failures, and connectivity issues, which can impact the overall efficiency of automated systems.
Signal degradation is one of the most common issues observed with FANUC PCBs. This can occur due to a variety of factors, including interference from nearby electromagnetic sources or physical damage to the PCB itself. To diagnose this, technicians can employ an oscilloscope to monitor signal integrity across the board. This tool allows for detailed analysis of signal waveforms, which can help identify degradation points and assist in determining appropriate remedial actions.
Component failures are another prevalent problem that affects FANUC PCBs. These failures can arise from age, overheating, or voltage spikes. When components such as capacitors or resistors malfunction, the entire board can exhibit erratic behavior. Utilizing a multimeter can help technicians check for continuity and measure the voltages across individual components, aiding in pinpointing any defective parts that may need replacement.
Connectivity issues can often stem from poor solder joints, corrosion, or damaged traces on a PCB. These problems can present a significant challenge, as they may not always manifest as visible damage. To diagnose connectivity concerns, a visual inspection complemented by the use of continuity testers is recommended. Additionally, reflowing solder joints or using conductive adhesives may improve connections on affected areas, restoring functionality.
By employing these diagnostic tools and techniques, technicians can effectively troubleshoot and address common issues with FANUC PCBs. Early identification and resolution of these problems are crucial to maintaining operational efficiency and prolonging the lifespan of essential automation components.
Maintenance Best Practices for FANUC PCB
Maintaining FANUC printed circuit boards (PCBs) is essential to ensure operational efficiency and longevity. As electronic devices, PCBs are susceptible to various factors that can impair their performance if not properly cared for. Implementing effective maintenance strategies can significantly reduce the likelihood of malfunctions and extend the lifespan of these crucial components.
One of the primary practices for maintaining FANUC PCBs is regular cleaning. Contaminants such as dust, dirt, and moisture can accumulate on the surface and within the connectors of the boards, leading to signal degradation or even complete failure. Use a soft brush or lint-free cloth to remove dust, and a suitable electronic cleaning solvent for any residue. It is important to ensure that the PCB is powered off and completely dry before re-engaging any connections.
Periodic inspections are equally crucial in maintaining the integrity of FANUC PCBs. Visual inspections should be conducted to identify signs of wear, such as discoloration, corrosion, or burned components. Additionally, it is beneficial to regularly check solder joints and connectors for signs of cracking or detachment. Early identification of potential issues allows for timely intervention, preventing extensive damage and costly repairs.
Environmental factors play a significant role in the maintenance of PCBs. FANUC PCBs should be housed in environments that avoid excessive heat, humidity, and exposure to corrosive substances. It is prudent to use enclosures that minimize environmental stressors and to adhere to specified temperature and humidity guidelines. Implementing temperature and humidity control systems can also provide an additional layer of protection for these delicate components.
In conclusion, proactive maintenance practices such as regular cleaning, periodic inspections, and attention to environmental conditions are critical for preserving the performance and reliability of FANUC PCBs. By adhering to these best practices, operators can maximize the efficiency and lifespan of their PCB systems, thereby ensuring optimal operational performance.
Applications of FANUC PCB in Industries
FANUC PCBs, renowned for their precision and reliability, find extensive applications across diverse industries, including automotive, electronics, and healthcare. In the automotive sector, FANUC PCB technology is integral to enhancing manufacturing processes. For instance, the use of robotics powered by FANUC PCBs enables seamless automation in assembly lines. This automation not only accelerates production rates but also significantly reduces the margin of error typical in manual processes, thereby improving overall vehicle quality.
In the electronics industry, FANUC PCBs are pivotal in the development and production of complex circuitry and devices. Their superior integration capabilities allow for the efficient management of intricate electronic systems, ensuring that components function harmoniously. As consumer demand for electronic devices grows, the reliability and efficiency delivered by FANUC technology facilitate meeting these market demands without compromising on quality. Moreover, the ability of FANUC PCBs to adapt to various electronic manufacturing environments demonstrates their versatility and critical role in driving innovation within the industry.
Healthcare is another significant sector benefiting from FANUC technology. Medical devices, robotics for surgical assistance, and automated laboratory equipment often incorporate FANUC PCBs for their precision and reliability. The demand for high accuracy in healthcare is paramount, and FANUC technology enhances the efficiency of diagnostics and treatments. For instance, automated systems powered by FANUC PCBs streamline laboratory workflows, leading to faster test results and improved patient outcomes.
As industries continue to evolve, the application scope of FANUC PCBs expands, facilitating advancements that enhance productivity and efficiency. The flexibility of FANUC technology enables the integration of cutting-edge solutions, making it an invaluable asset across various sectors. This adaptability ensures that FANUC PCBs remain at the forefront of industrial automation and smart technology development, driving progress in manufacturing and healthcare alike.
Future Trends in FANUC PCB Technology
The landscape of FANUC Printed Circuit Boards (PCBs) is evolving rapidly as new technological advancements are reshaping its component design and operational capabilities. One of the most significant trends is the advancement in materials used for manufacturing PCBs. Innovations in flexible and high-performance materials are enabling the production of lightweight and more durable boards. This shift is essential in applications where space constraints are paramount, as the automotive and aerospace industries continue to demand more efficient designs.
Another notable trend is the miniaturization of PCB components. As devices become smaller and more powerful, the need for compact electronic assemblies grows. FANUC is at the forefront of this trend, developing ultra-small PCB designs that maintain functionality without sacrificing performance. This miniaturization enhances integration within compact devices, thereby improving the overall user experience and device effectiveness.
Integration with the Internet of Things (IoT) is also transforming FANUC PCB technology. Smart PCBs equipped with sensors and communication capabilities can now connect seamlessly with other devices, allowing for real-time data exchange and remote monitoring. This connectivity fosters the development of intelligent systems that optimize workflows, increase efficiency, and reduce operational costs in manufacturing environments. The emphasis on IoT integration is set to revolutionize how machinery and electronic components interact in industrial settings.
Additionally, the incorporation of artificial intelligence (AI) into programming and operation processes is another forward-looking trend in the FANUC PCB sector. AI algorithms can enhance the precision and speed of PCB assembly, making it easier to identify defects and improve quality control. This integration not only refines production methodologies but also leads to a reduction in error rates during assembly. Overall, these advances reflect a commitment to innovation, ensuring that FANUC PCB technology remains relevant in an ever-changing technological landscape.
Conclusion and Final Thoughts
In summarizing our exploration of FANUC printed circuit boards (PCBs), it is evident that they play a critical role in the functionality and efficiency of a wide range of industrial applications. Understanding the intricate components and the technology behind FANUC PCBs is essential for engineers and technicians who work with automation and robotics. Such knowledge not only aids in the maintenance and troubleshooting of existing systems but also fosters innovations in design and integration in future projects.
The key components of a FANUC PCB, including microcontrollers, capacitors, resistors, and connectors, each serve distinct functions that contribute to the overall performance of electronic systems. By mastering the characteristics and interrelations of these components, professionals can ensure optimal operation and longevity of equipment. Furthermore, the applications of FANUC PCBs span diverse sectors, including manufacturing, automotive processes, and consumer electronics, thereby highlighting their versatility and importance in modern industry.
As technology continues to evolve, so must the skills and knowledge of those working within these frameworks. Engineers and technicians are encouraged to engage with additional resources, such as specialized training programs, industry conferences, and online forums. These platforms can provide deeper insights into the latest advancements in FANUC technology, as well as share best practices and troubleshooting strategies among peers in the field.
To conclude, a thorough understanding of FANUC PCBs not only enhances individual professional capabilities but also contributes to the advancement of industry standards. The insights, knowledge, and skills gained from this exploration set the groundwork for future endeavors in automation and robotics, paving the way for innovative solutions and improved operational efficiencies. By prioritizing education and engagement in this area, we can ensure that we are well-equipped to tackle the challenges of an ever-evolving technological landscape.