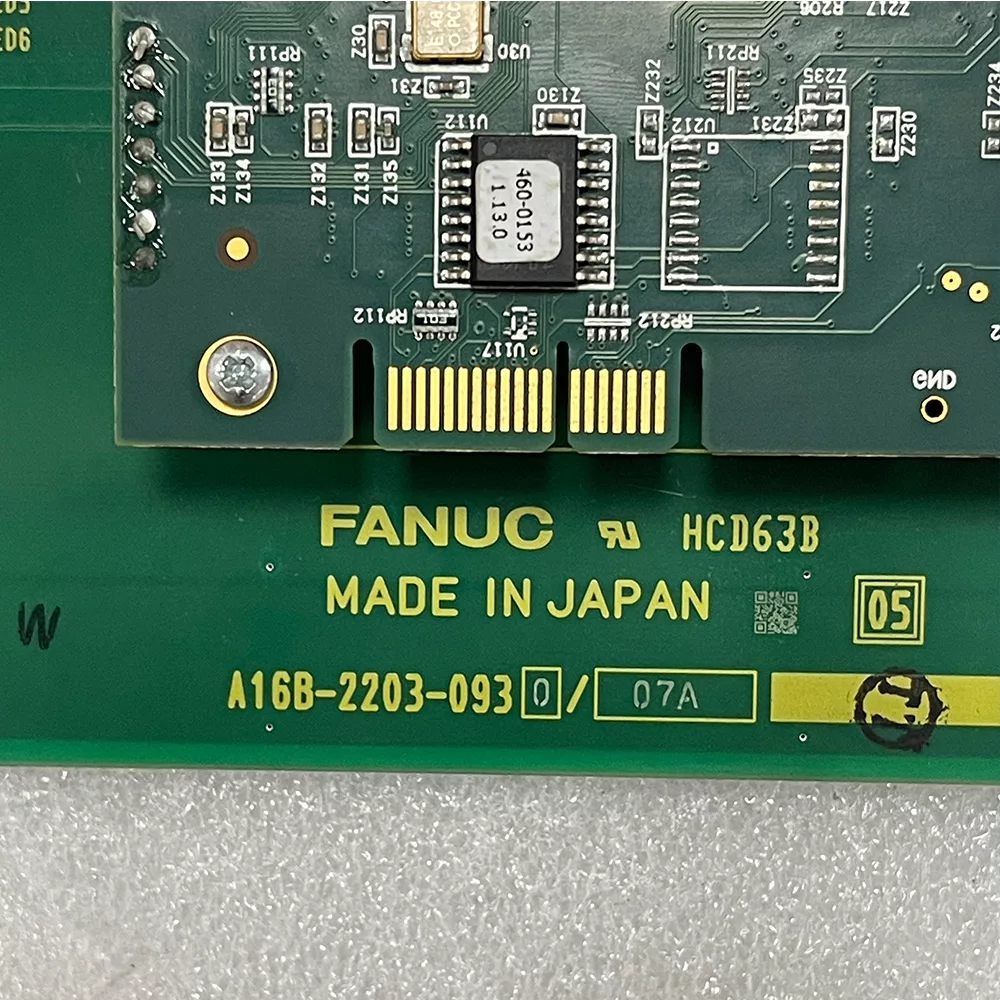
Understanding the Fanuc PCB Board: The Heart of Automation
Introduction to Fanuc and Its Importance in Automation
Fanuc, founded in Japan in 1956, has established itself as a premier manufacturer of industrial automation equipment, known for its cutting-edge technology and innovative solutions. As a pioneer in the field of robotics and CNC (Computer Numerical Control) systems, Fanuc has played a crucial role in shaping modern manufacturing processes. The company’s commitment to research and development has resulted in a wide array of products, including industrial robots, CNC controls, and machine tools, which have revolutionized various industries such as automotive, electronics, and aerospace.
The contributions of Fanuc to automation technology cannot be overstated. Its products are designed to enhance efficiency, productivity, and precision in manufacturing operations. With an emphasis on quality and reliability, Fanuc’s equipment is utilized globally, allowing businesses to automate repetitive tasks and streamline processes. Central to the functionality of these advanced systems is the PCB (Printed Circuit Board), which serves as the connective backbone for the electronic components embedded within Fanuc’s machinery.
The importance of the PCB in Fanuc’s automation solutions lies in its role in managing the electrical pathways that enable communication between various system components. This intricate network facilitates the processing of data, controls motor actions, and ensures the seamless operation of machinery. As automation continues to evolve, particularly with the integration of IoT (Internet of Things) and AI (Artificial Intelligence), the PCB’s significance in ensuring reliable functionality and performance cannot be underestimated.
In conclusion, Fanuc’s dedication to innovation and quality has made it a leader in the automation sector. Its products, underscored by robust PCB technology, not only enhance manufacturing capabilities but also push the boundaries of what is possible in automated processes. Understanding Fanuc and its technological advancements is essential for comprehending the future landscape of industrial automation.
What is a PCB and Its Role in Fanuc Equipment?
A printed circuit board (PCB) is a crucial component in electronic devices, serving as a foundational element that connects various electronic components. Within the context of Fanuc equipment, which includes robotics and automation machinery, the PCB acts as a sophisticated nervous system that facilitates communication between the different parts of the system. The PCB achieves this by providing the necessary circuitry for electrical signals to transmit between devices, thereby enabling the efficient functioning of equipment.
The primary role of a PCB in Fanuc automation is to house and connect microcontrollers, sensors, and actuators. By integrating these critical components, the PCB ensures that data is processed and relayed effectively, allowing for precise control over movements and operations. This is essential in manufacturing environments where precision and reliability are paramount. Through the intricate pathways and soldered connections on the PCB, electrical signals travel seamlessly, allowing for real-time interaction between different machinery and enabling quick responses to operational demands.
Moreover, the structure of a PCB allows it to accommodate various functionalities, making it adaptable to different applications within Fanuc technologies. Its design can vary from simple boards supporting basic functions to complex multilayered setups that manage sophisticated processes. Importantly, without a properly functioning PCB, the overall performance of Fanuc machinery would be significantly compromised, leading to potential downtimes and operational inefficiencies.
In sum, the PCB is central to the operation of Fanuc robotics and equipment, acting as a reliable medium for component connection and signal transmission. Its vital contribution cannot be overstated, as it directly impacts the efficiency and effectiveness of automation processes in various industrial settings.
Types of Fanuc PCBs and Their Specific Uses
Fanuc, a leader in automation and robotics, produces several types of Printed Circuit Boards (PCBs) tailored for various applications within their systems. Understanding these different PCB types is essential for leveraging the full potential of Fanuc’s automation solutions. These boards can be generally categorized into three main types: control boards, power supply boards, and interface boards, each playing a critical role in Fanuc products.
Control boards are vital components in any automation system. They manage and control the operational features of robots and CNC machines. These PCBs facilitate communication between the main processor and connected devices, ensuring precise execution of commands. For instance, Fanuc’s control boards can be found in robotic arms used in manufacturing, where they synchronize movements to carry out assembly tasks efficiently. Their reliability and performance directly impact the overall functionality and productivity of automated operations.
Power supply boards are another essential type of PCB within Fanuc’s offerings. These boards convert electrical power from the mains into a usable format for different components of robotic systems. They are critical in ensuring that robots and automation equipment receive the correct voltage and current levels, which contributes to stable operation and longevity of the devices. In applications such as injection molding or part machining, power supply boards help maintain consistent power delivery, reducing the risk of errors or downtime.
Lastly, interface boards serve as the linking bridge between various electronic components and the control system. These PCBs usually contain connectors and communication ports that allow for the integration of sensors, actuators, and other peripherals. For example, in automated assembly lines, interface boards enable seamless interaction between robots and other machinery, which is vital for efficient operation. With the right interface board, Fanuc systems can communicate effectively, enhancing their adaptability and performance in multiple environments.
Manufacturing Process of Fanuc PCBs
The manufacturing process of Fanuc PCB boards involves a meticulous approach that ensures high-quality standards and outstanding performance in automation applications. The foundation of this process begins with the selection of appropriate materials. Typically, Fanuc utilizes high-grade FR-4 fiberglass epoxy resin for the substrate, which provides excellent electrical insulation and mechanical stability. Additionally, copper is employed for the conductive pathways, chosen for its superior conductivity and reliability.
Design considerations play a critical role in the fabrication of these complex PCBs. Engineers at Fanuc meticulously design each board to accommodate the specific functionalities required for various automation tasks. This includes considerations of size, layer count, and component placement to optimize signal integrity and reduce electromagnetic interference. Computer-aided design (CAD) software is often used to create intricate layouts that precisely dictate how the components will be arranged and connected.
The manufacturing process itself typically follows several key steps. Initially, a PCB prototype is created, allowing for testing and validation of the design. Once approved, the process transitions to the production phase, which includes the following critical steps: layering, etching, drilling, and solder masking. During layering, multiple sheets of material are stacked together according to the design specifications. The etching process then removes excess copper to form the desired circuitry. Drilling follows, creating precise holes for electronic components, which are then inserted and soldered into place.
Throughout the manufacturing process, Fanuc adheres to stringent quality control measures and industry standards such as IPC-A-600 to ensure that the PCBs meet the reliability and performance expectations synonymous with the brand. Each board undergoes rigorous testing before being deployed in automation systems, aligning with Fanuc’s commitment to delivering exceptional technology and maintaining industry leadership.
Common Issues and Troubleshooting Fanuc PCBs
Fanuc PCBs, as integral components of automation systems, are susceptible to a range of problems that can hinder performance and reliability. One of the most prevalent issues encountered is electrical failure, which may manifest as erratic behavior of connected machines or complete system shutdowns. These failures can result from various factors, including short circuits, component wear, or improper voltage levels. To diagnose electrical faults, one can employ multimeters and oscilloscopes to measure voltage, current, and signal integrity across the PCB. Identifying these irregularities can often illuminate the root cause of the issue.
Another common problem pertains to physical damage, which can occur during installation, maintenance, or operation. This damage may include cracked solder joints, burnt traces, or any form of mechanical injury. Visual inspections play a crucial role in this area; examining the PCB for visible signs of wear or damage can provide immediate insights. In cases where damage is identified, a judicious approach is recommended. If the damage is minor, it may be possible to repair it with soldering or patching techniques. However, extensive damage often necessitates a complete replacement of the PCB.
When troubleshooting Fanuc PCBs, it is essential to be systematic, beginning with the most obvious issues before progressing to more complex diagnostics. Utilizing diagnostic tools provided by Fanuc, such as software tests and LED indicators, can be very beneficial in pinpointing failures. Lastly, if the issues persist despite careful troubleshooting, consulting a professional technician who specializes in Fanuc systems is advisable. Their expertise may be crucial in resolving complex malfunctions that require high-level intervention or specialized tools. A proactive approach to monitoring and maintaining Fanuc PCBs can greatly enhance longevity and operational efficiency in automation systems.
Maintenance Tips for Fanuc PCBs
Proper maintenance of Fanuc PCBs is crucial to ensure their longevity and reliability in various automation applications. One of the key aspects of PCB maintenance is handling. Always handle the printed circuit boards with care, avoiding direct contact with the component leads and traces to prevent damage. It is advisable to use anti-static wrist straps and gloves to minimize electrostatic discharge which can impair the functionality of the board.
Cleaning is another essential aspect of PCB maintenance. Ensure that you use appropriate cleaning agents that are specifically designed for electronics, as harsh chemicals can damage both the board and its components. Isopropyl alcohol is preferred because it evaporates quickly and leaves minimal residue. Utilize a soft brush or lint-free cloth to gently clean the surface, thereby avoiding any abrasive materials that could scratch or damage the board. Pay special attention to connectors and solder joints, as these can accumulate dirt and oxidation over time, impacting performance.
Furthermore, environmental considerations play a significant role in PCB maintenance. Fanuc PCBs are sensitive to adverse conditions such as humidity and temperature fluctuations. Store and operate the boards in environments with controlled temperatures and low humidity to reduce the risk of corrosion or component failure. Housing the PCBs in dust-free enclosures can also provide an additional layer of protection against contaminants.
Regular inspections are vital for early detection of potential issues. Look for signs of wear and tear, such as discoloration, burns, or unusual smells. By identifying problems early, necessary interventions can be implemented promptly, thus safeguarding the integrity and performance of Fanuc PCBs. These maintenance tips can greatly enhance the operational life of the boards, ensuring effective automation processes for the long term.
Upgrading and Replacing Fanuc PCBs
Upgrading or replacing a Fanuc PCB board is a critical task that requires thorough planning and consideration to ensure operational continuity. The first factor to consider is compatibility between the existing equipment and the new PCB. Different generations of Fanuc products may utilize distinct communication protocols and connections which must be meticulously matched. Before procuring a replacement, it’s essential to verify part numbers and consult the manufacturer’s guidelines or technical documentation. This step is vital to avoid deploying hardware that may not integrate seamlessly with the existing setup.
When selecting replacement parts, it is advisable to source components from reputable suppliers to guarantee authenticity and optimal performance. Counterfeit or inferior-quality PCB boards may lead to performance degradation, which can disrupt the workflow and potentially cause operational downtime. Additionally, it is beneficial to consider the versioning of software that accompanies the new PCB; compatibility between the hardware and software is crucial to facilitate a trouble-free transition.
Best practices for upgrading or replacing Fanuc PCBs also include a thorough operational impact assessment. Prioritize planning the upgrade during low-traffic hours or scheduled maintenance periods to minimize disruption to ongoing processes. Utilizing backups of existing data and configurations can safeguard against potential loss during the transition. As part of the installation process, rigorous testing is necessary to confirm that the new PCB operates correctly within its environment. This includes running diagnostics to ensure all functions perform as expected without any glitches.
Informing and training staff on new operational procedures post-upgrade plays a crucial role in achieving a successful transition. As technology continues to evolve, the careful upgrade or replacement of Fanuc PCBs ensures that automation processes remain efficient, reliable, and up to date with the latest advancements in control technology.
Future Trends in Fanuc PCB Technology
The landscape of Fanuc PCB technology is rapidly evolving, influenced by multiple emerging trends that reflect the advancements in both design and manufacturing processes. As industries move towards increased efficiency and lower production costs, the demand for sophisticated printed circuit boards (PCBs) has risen significantly. One notable trend is the ongoing miniaturization of PCBs, which is essential for modern automation solutions. Smaller components allow for a denser arrangement of circuitry, enabling enhanced functionality within compact systems. This propensity for miniaturization supports the creation of smaller robots and automation devices, which can operate in environments previously deemed unsuitable for traditional-sized equipment.
Integrating smart technology into Fanuc PCBs represents another pivotal trend shaping the future of automation. With the rise of the Internet of Things (IoT), PCBs are being designed not just for basic control functions but also to facilitate data exchange and real-time monitoring capabilities. This evolution enables Fanuc systems to perform advanced functions, such as predictive maintenance and adaptive learning. In this way, smart technology transforms traditional automation paradigms, enhancing operational efficiency and decision-making capabilities.
Moreover, the impact of Industry 4.0 on PCB development cannot be overstated. This new industrial revolution encourages greater interconnectivity and automation across all manufacturing stages. As Fanuc’s role in this framework expands, the importance of compatible PCBs that can seamlessly integrate with various systems grows. Innovations in automated manufacturing practices, such as additive manufacturing and advanced surface mount technology, are likely to streamline PCB production. Consequently, the integration of these cutting-edge methodologies with Fanuc’s existing technologies could significantly improve production flexibility and time-to-market.
In conclusion, the future trends in Fanuc PCB technology point towards a more compact, intelligent, and interconnected approach to automation, with advancements in miniaturization, smart integration, and Industry 4.0 shaping the way forward.
Conclusion: The Vital Role of Fanuc PCBs in the Future of Automation
As the automation landscape continues to evolve, Fanuc PCB boards emerge as indispensable components that drive advancements in industrial processes. These printed circuit boards are not merely electronic elements but the backbone of modern manufacturing technologies, ensuring enhanced functionality and operational efficiency. The integration of Fanuc PCBs facilitates a seamless flow of information between different automation systems, allowing for real-time data analysis and feedback loops that are essential for improved productivity.
The reliability of Fanuc PCB boards plays a crucial role in minimizing downtime within manufacturing environments. By providing consistent performance and durability, these components are engineered to withstand the rigors of industrial settings. This reliability translates directly into increased machine uptime and a reduction in maintenance costs, making Fanuc PCBs not just a component but a strategic investment for any manufacturing facility. Moreover, their advanced design enables compatibility with a wide range of automated tools and machinery, fostering a more integrated approach to industrial automation.
Looking ahead, the role of Fanuc PCB boards in the future of automation becomes even more significant as industries embrace the Internet of Things (IoT) and smart technologies. With their ability to support advanced connectivity solutions, Fanuc PCBs are poised to enable smarter operations where machines communicate and collaborate in real time. This transition towards interconnected systems will undoubtedly propel the evolution of manufacturing practices, establishing new standards for efficiency and innovation.
In conclusion, the importance of Fanuc PCBs cannot be overstated. Their contribution to enhancing reliability and efficiency in industrial automation sets the stage for future breakthroughs in manufacturing. As we continue to navigate the complexities of automation technology, understanding the critical role of these circuit boards will empower us to appreciate their impact on productivity and operational excellence.